Quality assurance and quality control are two methods of planning and implementing structured methods in a work process to ensure that products are created with the highest possible quality and with the smallest number of defects and problems.
Quality Assurance
Quality assurance (QA) refers to the planned and systematic activities implemented in a quality system to fulfill the quality requirements for a product or service It is a systematic measurement compared to a set standard, with process monitoring used to prevent errors. This can be contrasted with quality control, which is focused on process outputs. Two key principles of QA are:
- Fit for purpose: The product should be suitable for its intended purpose.
- Right the first time: Mistakes should be eliminated.
QA includes managing the quality of raw materials, assemblies, products, components, services related to production, management processes, production processes, and inspection processes. The critical takeaway here is that QA equates to process observations.
Quality assurance is measured through failure testing and statistical control. Failure testing determines the stress levels under which a product will fail by exposing it to unanticipated stresses, like intense vibration, temperature, and humidity. Stress testing uncovers problems that can be fixed with simple changes to improve the product. Statistical controls ensure that an organization is producing quality products at the lowest possible defect rate. Many organizations use Six Sigma levels of quality, so the likelihood of an unexpected failure is less than four in one million.
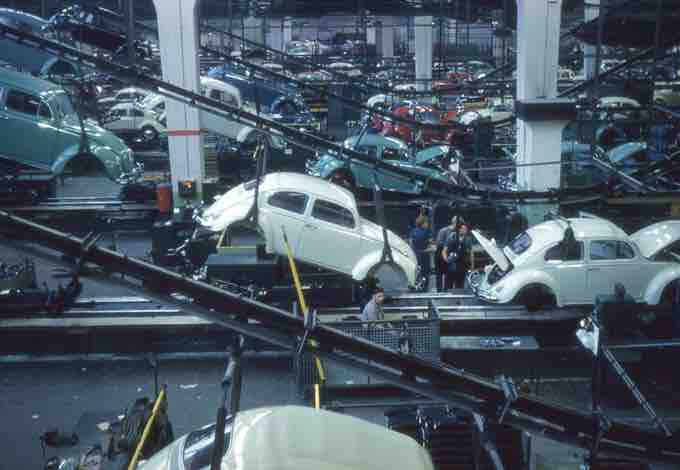
Assembly line and quality control
Many processes, such as assembly lines, help ensure quality assurance and control by streamlining the production process.
Quality Control
Quality control (QC) is the process of testing finished products to uncover defects and reporting the results to management, which makes the decision to allow or deny product release. It differs from quality assurance, which attempts to improve and stabilize a product, and eliminate any flaws, during production.
Controls also include product inspection: every product is examined visually before the product is sold into the external market. Inspectors are provided with lists and descriptions of unacceptable product defects, such as cracks or surface blemishes. Efficient quality control depends on top-notch visual examination of products, employee training, and organizational culture.
Quality control and quality assurance work together to make sure that companies produce products that have the lowest possible error rate, so there will be fewer customer complaints and no need to rework the product in the future.
Outsourcing
Due to the high degree of vendor dependency, many corporations find their manufacturing processes are conducted outside of their organization. This can lead to difficulties in maintaining process quality. In this situation, a corporation needs to invest in QC professionals to maintain organizational standards. The primary takeaway here is that QC is not simply an internal concern for many businesses, but also an external vendor selection criteria.